

Direct3D 9 or compatible graphics card (Direct3D 11 or higher recommended).Xeon E3 or Core i7 or equivalent, 3.3 GHz or greater.Microsoft Excel 2003 or later software for iFeatures, iParts, iAssemblies, thread customization, and spreadsheet-driven designsįor complex models, complex mold assemblies, and large assemblies (typically more than 1,000 Parts):.
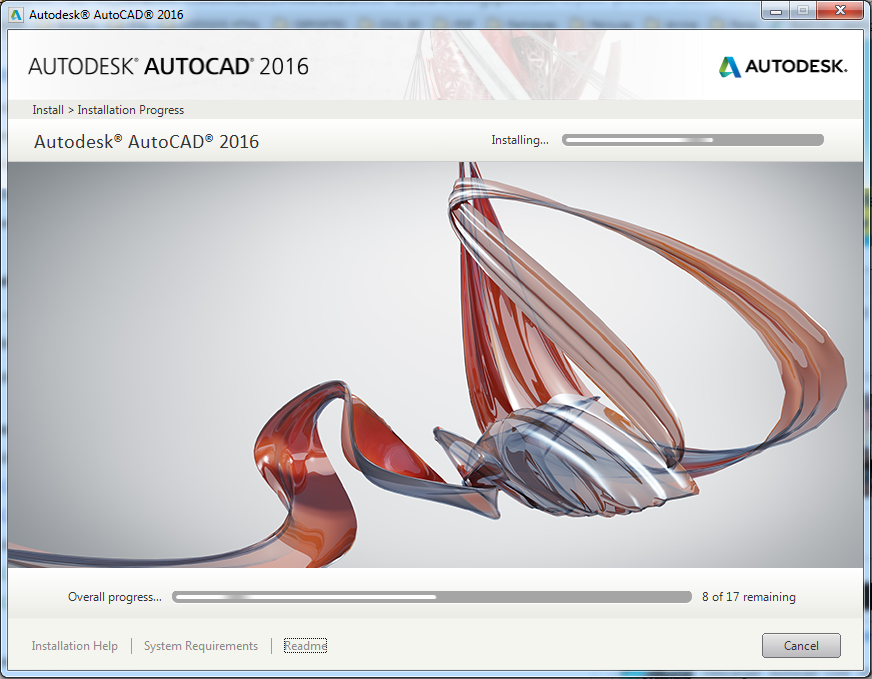
Microsoft Internet Explorer 6 or later (.NET Framework Version 4.5 web browser).Microsoft Direct3D 9 or compatible graphics card (Microsoft® Direct3D 11 or higher recommended).1,280 x 1,024 or higher screen resolution.4 GB RAM minimum for less than 500 part assemblies (8 GB recommended).Intel Pentium 4, AMD Athlon 64 with SSE2 technology, 3 GHz or greater, or AMD dual-core processor with SSE2, 2 GHz or greater recommended, or Intel Xeon E3 or Core i7 or equivalent with SSE2, 3.0 GHz or greater.Windows 7 (32-bit minimum, 64-bit recommended) or Windows 8 64-bit operating system.Minimum requirements (more info)įor general part and assembly design (typically fewer than 1,000 parts): Anyway to use the simulation in the CAD is to locate areas where the stress is high and that the user should be based on a safety factor that talk about that later. These are considerations that should be taken into account when the stress analysis in Autodesk Inventor is done and this is where users must analyze whether these assumptions affect greatly to their simulations, if the user believes that invalidate his analysis completely then it would a better idea to consider using a more complete simulation package such as Autodesk simulation Mechanical. For a linear static analysis that make most CAD packages, the temperature does not enter into consideration. Most materials change their behavior when applied temperature.The load applied is completely static and slowly apply the load vector will always have the same direction and magnitude, and no shock effects are considered.That is, although the stress in the part exceeding the elastic limit, the performance of the material will remain linear. The behavior of the material used will always be linear.Friction and stress are linearly proportional to the load.Then I make a list of what is assumed in the simulation: The intention is to talk about things that Inventor is taking to perform the simulation and also what we are saying to us as a result users provided by the software. I like to talk about the simulation capabilities that comprise Autodesk Inventor Professional for embedded for CAD users have obtained an approximate result indicating their behavior on their part or product certain conditions.
